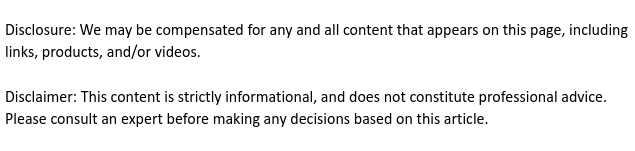
If you’re a law student interested in practicing in the area of manufacturing law, then it’s in your best interest to familiarize yourself with the basics of manufacturing regulatory compliance. You’ll need to be well-versed in everything it entails to offer quality representation to your future clients. This read will provide valuable information about all you need to know about regulatory compliance in the manufacturing industry.
1. Why Manufacturing Regulatory Compliance Is Important
Manufacturing regulatory compliance is the adherence to specifications, guidelines, regulations, and laws pertinent to an organization’s operations. These regulations may be international or domestic and encompass various compliance challenges. Violations sometimes carry legal repercussions, such as expensive federal penalties or removing a product from the market.
These infractions not only carry possible fines for the manufacturer, but they also carry a risk of serious accidents or significant property loss. Adhering to regulatory standards guarantees the safety of products and protects the humans, animals, property, and equipment that are part of the product’s environment.
Quality systems are becoming an integral aspect of many businesses. Part of this is that customers are likelier to do business with organizations that use an accredited quality system. Here’s where Internationally recognized standards like ISO 9000 come in.
Few manufacturers overall don’t operate in this realm. Regulatory compliance is a distinct entity. It presents a legal obstacle course that necessitates the help of a professional to navigate it successfully. For example, in the case of technology patents, technology patent attorneys offer valuable legal help.

2. The Potential Impacts of Non-Compliance
Non-compliance is not adhering to or following established rules, obligations, standards, or regulations. It may take on various contexts, such as ethical, legal, organizational, or industry-specific requirements. It may involve a manufacturer deliberately disregarding or violating set guidelines or unintentionally failing to meet expectations.
Regulatory non-compliance can have costly consequences. For example, it can result in jail time, lost production, property damage, and, in some cases, worker deaths and injuries. Even though compliance increases productivity and shields organizations from inuring heavy penalties, most still consider it an expense rather than an investment. As a result, businesses tend to understaff their compliance teams and limit or ignore the acquisition of compliance data, services, and software, which often results in them dealing with leading process servers.
However, the costs and risks associated with non-compliance easily outweigh that of investing in compliance initiatives. Companies that downplay the significance of proactive compliance often wind up footing the bill, but in the form of fines, damaged reputations, and delayed product releases. Penalties for failing to adhere to manufacturing regulatory compliance standards can come in multiple forms, including prison, extra barriers to approval, limitations on activities, and financial fines.
Even when a penalty isn’t given, investigations by a government agency can cost several hours of labor and any legal and contractor expenses. Depending on the seriousness of the infraction, legal consequences for non-compliance could be severe. Regulatory bodies can conduct inquiries, apply sanctions, and maybe cancel licenses or permits, contingent on the severity. Non-compliance can also result in reputational damage. This often manifests in customers, investors, and stakeholders losing trust in a manufacturer, a tarnished brand reputation, a drop in stock prices, and an overall decline in sales.
3. The Scope of Manufacturing Law
Regulations and statutes about the manufacturing sector are known as manufacturing laws. The manufacturing sector in the United States has declined over the past 50 years. Yet, despite this, it is still a significant contributor to the country’s economy and an important practice area of the legal system. Every year, the manufacturing sector adds around $2 trillion to the nation’s GDP, according to HG.org. As a result, claims concerning manufacturing procedures often attract a large financial risk.
No product can get to the market without the input of humans. This implies that labor and employment-related issues may arise at any time. It’s common to see manufacturers being targeted for organized labor issues such as strikes, collective bargaining, and unions.
Marketing and advertising is another area of manufacturing regulatory compliance law that manufacturers and legal professionals must be aware of. The Federal Trade Commission (FTC) is responsible for monitoring these matters. It issues regulations that specify what can and can’t be said in commercials, prohibits deceptive and false claims, sets guidelines for depictions of ‘green’ products, and other things.
Consolidation has been a common practice for manufacturers for several years due to the evolving nature of the American manufacturing landscape. Therefore, laws on manufacturing also tend to affect business formation, mergers, and governance. When a business buys out or merges with another, it could also take on the liabilities for the products it produced before the merger and the assets it already owned.
Product liability is another major issue for some manufacturers. For example, automakers often deal with cases of alleged product defects. Such lawsuits can be quite profitable for plaintiffs’ attorneys. These types of cases have given birth to an entire industry in the legal profession. Things such as carrier surcharges are generally not covered in manufacturing law.

4. What to Know About Manufacturing Certificates
Manufacturing certifications are incredibly useful. Each provides great prospects and strong customer appeal. They support environmental preservation, worker safety, quality improvement, and increased reliability. Above all, manufacturing certificates offer reassurance that a company is adhering to the right legal and customer criteria, whether they deal with plastic random packing or any other area. A certification is an indicator of expertise.
There are several options for certification, whether an individual works in or is considering a career in manufacturing. There isn’t a single certification; instead, they often belong to one of two groups. The first one is a trades-related diploma or certificate. One only receives this after completing extensive professional training and work experience in a specific trade, like an electrician.
The other category pertains to a particular facet of a broader spectrum of industries. Every business that manufactures products is included in this group. The training covers the details of a particular part of this process. This is where you’ll find positions like engineering technicians, logistics specialists, quality certifications, and safety and health instructors.
5. Preventing Product Liability Cases
Product liability refers to products, such as air bag jacks, with flaws that harm the consumer. Every state has its own tort law negligence-based product liability statute. Under product liability law, all parties involved in the transaction are accountable for any harm. This includes everyone from the manufacturers and assemblers to the retailers and wholesalers. Sometimes, even small shops that sell the complete product may be held liable.
As a law student, you should know that holding the right insurance is the first line of defense against lawsuit expenses due to manufacturing regulatory compliance issues. However, the best course of action is to avoid a court date completely. Some supply chain management best practices can help minimize the risks and ensure client and customer safety.
For example, if a business manufactures or designs digital or physical products, it should ensure the testing procedures are sound before the general public gets their hands on the goods. The CPSC requires regulated product manufacturers to conduct in-house or third-party laboratory testing on their products. Children’s product designers and manufacturers must perform product troubleshooting in a CPSC-certified laboratory. Quality assurance systems and software are helpful resources for identifying product defects before they become serious issues.
Manufacturers should prominently display warning labels on products that pose a safety hazard. They should be as detailed as possible and include all potential risks and how consumers can avoid them. It’s also a good idea to include warnings in several languages.
Defective equipment also often causes product flaws. Staff should be dedicated to regularly inspecting, testing, and cleaning manufacturing machinery. Faulty machines can also result in employee injuries and lead to workers’ compensation lawsuits and claims.

6. Maintaining a Safe Manufacturing Environment
Workers in the manufacturing sector often perform dangerous tasks like rigging and heavy lifting, raw material assembling, metal cutting, welding, and soldering. Besides that, hazardous radiations, pressurized gasses, and magnetic fields can all harm a worker’s health. In fact, according to Industrial Safety & Hygiene News, there are about 150 occupational fatalities in the United States every day.
The key to maintaining a safe manufacturing environment and ensuring manufacturing regulatory compliance is identifying potential occupational hazards and implementing measures to prevent workplace accidents. Risk assessment keeps manufacturers aware of the dangers in their facility. It also helps them determine which equipment needs professional attention, like hydraulic machinery repair. A plant assessor is best positioned to create a risk assessment plan that lists every danger connected to each manufacturing subprocess.
Manufacturing plants are often unorganized and messy. Cluttered work areas with greasy or wet floors combined with stinger leads, power cords, or cylinder hoses lying across walkways increase the likelihood of workplace accidents. It’s good practice to keep workstations, aisles, and pathways clear of anything that might lead to accidents like falls, fires, or slips.
When on the factory floor, manufacturing workers should always have protective gear to lower their injury risk. OSHA now mandates metal workers to wear PPE like full body suits, respirators, hard hats, earplugs, gloves, shoes, and safety hoods.
Workplace safety should be part of the design of every manufacturing facility. For example, plasma-cutting machines and plate- and sheet-forming equipment feature guards and other safety features to safeguard workers’ fingers. Workers may easily lose their fingers if these guards don’t fit correctly.
7. Keeping Up With OSHA Requirements
OSHA is one of the main bodies determining manufacturing regulatory compliance standards. It provides guidelines for ensuring health and safety in a facility, such as when using equipment like rigging wire ropes. There are some resources that a manufacturer can use to stay compliant. For example, a free online resource such as the OSHA Quicktakes bi-weekly magazine provides new injury statistics, safety tips, and regulations.
The OSHA Law Blog is also helpful, providing information about workplace safety developments, rules, and enforcement. The Federal Register is another great place to get information on OSHA standards. It publishes regulations when they’re changed or when there are deletions, corrections, and insertions.

8. Why Quality Assurance Is Essential
Quality Assurance in manufacturing, like UV equipment manufacturing, describes the processes manufacturers use in their quality management system to ensure consistent quality levels for the products they produce. It’s often paired with quality control to guarantee that customers get high-quality products free from unexpected flaws. Manufacturers control product quality using quality assurance as opposed to quality verification. In every manufacturing setting, quality assurance is vital. Still, it’s especially crucial for some manufacturers, like those in the automobile sector and suppliers of high-precision parts, since a low-quality standard might lead to injury or even death.
Since QA uses a proactive approach, it helps prevent quality issues and helps ensure manufacturing regulatory compliance. This makes it possible for manufacturers to realize significant cost savings since they don’t have to account for as much in returns, scrap components, and other byproducts of low-quality items. When producers use efficient quality assurance processes, customers obtain better products consistently and on faster timelines. Since there’s a decreased chance of obtaining a substandard product, customers can benefit from increased customization and innovation later because more resources are available for these tasks.
9. How Compliance Can Improve Efficiency
For businesses of all sizes, compliance with industry regulations is essential in today’s fast-paced environment. Veritas reports that 56% of firms have experienced cybersecurity intrusions in the last year. Compliance solutions have become an instrument for increasing efficiency and streamlining processes for different businesses, including traffic deck coating services.
These solutions include a broad spectrum of software and services that help businesses manage risk, ensure ethical behavior, and comply with regulations. Compliance solutions help organizations save time, reduce mistakes, and keep current with laws by automating processes like audits, reporting, and document management with compliance automation technologies. Besides that, they offer a unified platform for department-to-department collaboration and communication, improving company accountability and transparency. As manufacturing regulatory compliance keeps getting complex, compliance solutions allow for a proactive approach to ensuring compliance, avoiding penalties, and protecting a company’s reputation.
10. Preparing for Future Regulations
Regulations are always changing as technological advancements arise and new manufacturing processes and equipment like palletizing robots emerge. Proactively preparing for future regulations is the best way to ensure a manufacturer stays compliant. Regular compliance training for employees across all levels is a great resource. It’ll make it possible to anticipate future regulatory changes.
Manufacturing regulatory compliance ensures that the products that get to the end users are of the highest quality and are safe. Besides that, non-compliance poses some serious consequences for manufacturers. As a law student, you’ll be wise to pursue manufacturing law as one of your practice areas. The demand will always be there.